System configuration chart
Quality inspection management system.
System's scale
Quality Inspection Center Version
- Input Windows: 35
- For the internal processing: 12
- Print (Label): 4
- Print (Form): 7
- Master input screen: 7
- SQL: 131
- Macro: 9
- Development started: May, 2012
- Full operation: January, 2013
Factory Version
- Input Windows: 36
- For the internal processing: 10
- Print (Label): 5
- Print (Form): 7
- Master input screen: 4
- SQL: 91
- Macro: 6
- Development started: May, 2013
- Full operation: January, 2014
- Quality inspection management system Ver2(Inspection Center version, Factory version) Development started: May, 2014
- Quality inspection management system Ver2(Inspection Center version, Factory version) Full operation: September, 2014
System summary
Quality inspection management system
Chilled Food System to manage quality inspection (Bacteriological testing, etc.) operations (Minced fish meat (Hanpen, Chikuwa, Satsuma-age, etc.) Household dishes). By developing the system, we became able to share information between the Quality Inspection Center and the quality inspection data (bacteriological inspection data and progress management) at our Product Development Department / Purchase Department / HQ quality management division/ Factories.
Number of users of the Quality Inspection Center and Product Development Department.
- ・Quality Inspection Center (Funabashishi, Chiba): 8 people
- ・Product Development Department , Purchase Department, Headquarters, and three branch offices: 60 people
- ・Quality control unit of the HQ and 6 domestic factories (*) : 50 people
- • Top screen
- • Input screen for inspection request
- • Inspection result input screen (microbial test)
- • Inspection result input screen (senses/preservation test)
- • Pass or fail determination screen
- • Master maintenance screen
Purpose of the system development
We enhance manufacturing management and quality and sanitation management for the products our company handles, with safety and security as the top priority, so that our customers can know they are eating very safe foods.
For the quality inspection operations of our products, the quality inspection data has been managed at the Quality Inspection Center and at 6 domestic factories independently, but we did not have a centralized management of the quality inspection data for the whole company.
Moreover, it was taking extra time for the Quality Inspection Center to get the inspection results from the Product Development/Purchase Departments because of the need to communicate with those divisions by telephone and/or by E-mail.
We then began to consider the introduction of a new system, first to improve the operational efficiency of the Quality Inspection Center and to get the quality inspection data from the Product Development / Purchase Departments promptly.
For the system development, we examined the following points.
- 1) Utilizing the assets we have already realized with the conventional system. (Excel + Macro)
- 2) The efficiency improvement in quality inspection operations (real time output of the inspection result chart, reduction of operational time by reducing the office workload).
- 3) Seamless information sharing between the Quality Inspection Center and Product Development/ Purchase Departments.
- 4) Budget feasibility without compromising functional, operational, and cost-effective aspects.
- 5) Systematizing of the Quality Inspection Center first and then the domestic factories.
- 6) Feasibility to develop and deploy new systems for better solution of the various works and processes in future after centralized quality inspection data management achieved.
Effect after the introduction
By developing a system with dbSheetClient, we established a system which can cope with multiple business bases between the Product Development/ Purchase Department/ Headquarters Quality Inspection Division and the Quality Inspection Center in accordance with the operational flow of [inspection request] » [accept inspection order] » [input inspection result] » [report results].
At the Quality Inspection Center:
- 1) The bar code label with the inspection number, which is issued at the time of accepting the inspection order and to be attached to the goods and devices to be inspected (Schale, etc.), is related to the bar code management of the inspection object to avoid mistakes of handling the wrong goods, and anyone can make a correct input/aggregation of the inspection result by reading the bar code with the bar code reader.
- 2) Since we need to cope with the inspection items for the various inspection objects of the chilled foods, we made a system to change the inspection items automatically by switching the classification name of the goods (minced fish meat products, household dishes, etc.), to conduct necessary inspection items required for each of the various products without omitting the necessary inspection item.
In former systems we often omitted necessary inspection items for each product, and later received telephone calls for verification and/or modification. Since there is no more inquiry for such issues, we could improve operational efficiency dramatically. - 3) Since the Product Development/Purchase Division can check the delivery status of the inspection goods, the progress status of the inspection, and reference to the inspection result all on the inspection system screen, it eliminated the necessity for the Quality Inspection Center to deal with inquiry from those departments by telephone or E-mail.
- 4) Our busy season is from October to the end of the year for both inspection jobs and paperwork: as the inspection job increases, so does the paperwork.
By the system development with dbSheetClient this time, it almost eliminated the post inspection works (inputting of the inspection results and paperwork for making the result sheets). The timely delivery of the result and overtime work cost reduction are highly appreciated in the offices.
We can now use the reduced manpower/hours to inputting and paperwork for sanitation management improvement, detailed data analysis, and searching true causes for various problems.
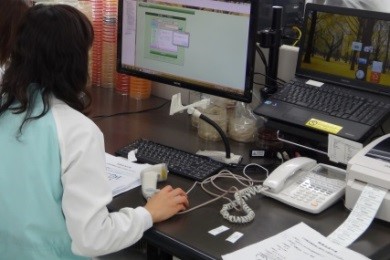
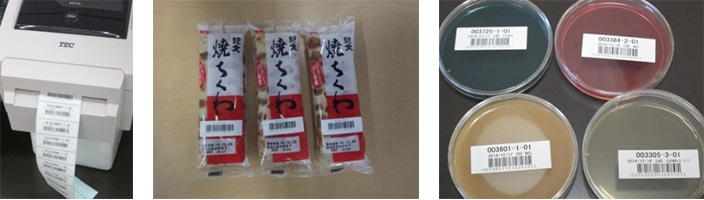
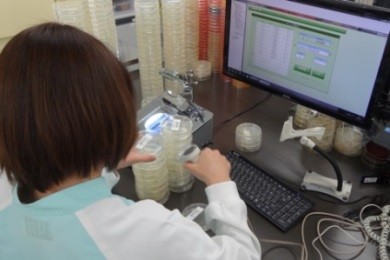
At the Product Development/Purchase Division,
- 1) In the past, inquiry for the inspection progress has been made by telephone and/or E-mail, but now after the system development, you can check the progress status of the requested product for inspection by yourself and do not need to bother the Quality Inspection Center.
- 2) You can check the real time comprehensive evaluation of the inspection result on the system, and do not need to inquire about it to the Quality Inspection Center.
The Quality Inspection Center conducted more than 2000 cases of inspection on the quality inspection management system in the year of 2013. We are very happy that we, as the Quality Inspection Center, could introduce and build the long-sought new system and have achieved a remarkable operational result.
We appreciate Newcom, Inc. who accommodated our request of specification changes during the system development willingly, for our specification involves rather complex features.
Moreover, in the year 2013, we developed a factory version quality inspection management system to deploy the system for the entire domestic factory's quality management office (quality inspection office).
Before that, we used to manage the quality inspection data of the factories manually and/or partly by Excel based database, which is often different from factory to factory. It is now developed into the system with an integrated database.
In each factory, you need a system to input data of mass inspections efficiently and without mistakes. We asked Newcom to develop input windows which incorporated the requests of the local factories.
In the year 2014, we added the new system features for Quality Inspection Center and for the factory version. For the factory version, what used to be manually handled such as forms for quality confirmation has been improved to be outputted from the inspection system data, and daily inspection data are automatically aggregated and the result of the inspection can be outputted from the system.
In the Quality Inspection Center version, we have developed a system to automate prompt e-mail notice of inspection errors and a system for generating error reports and authorization and confirmation of receipt of them for prompt handling.
Since the factory version started operating, over 100,000 cases annually of the quality inspection data of the domestic factories (some factories are still preparing for the introduction), are now under a centralized management.
Bacteriological examinations; indispensable everyday tasks
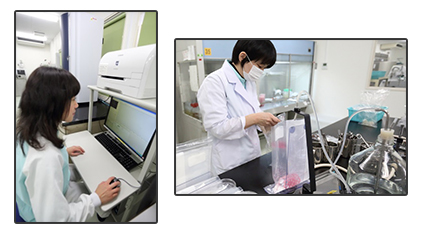
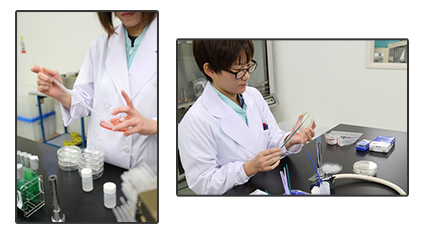
For customer’s safety and satisfaction; the commitment to Food Safety is Kibun’s motto.
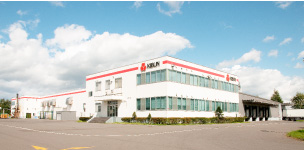
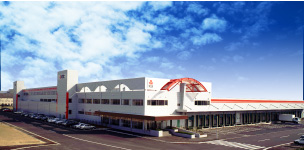
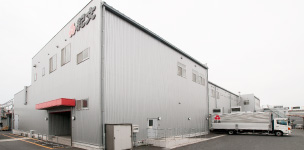
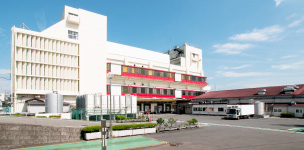
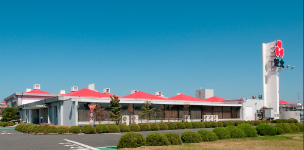
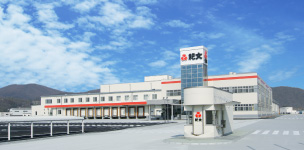